Introduction to Aerospace Grease Space Equipment
The field of aerospace engineering is both vast and intricate, requiring the highest levels of precision, reliability, and durability. One critical component within this domain is aerospace grease, a specialized lubricant designed for space equipment. Aerospace grease’s role is often underestimated, yet it is essential for ensuring the proper functioning of mechanical systems in extreme conditions. This article delves into the world of aerospace grease, exploring its composition, applications, and the stringent standards it must meet to be effective in the harsh environment of space.
Understanding Aerospace Grease
Aerospace grease is a type of lubricant specifically formulated to meet the challenging conditions encountered in aerospace applications. Unlike conventional lubricants, aerospace greases must endure extreme temperatures, intense pressure differentials, and vacuums, all while maintaining their physical properties. The unique demands of space travel necessitate special considerations in the formulation of these greases.
Generally, aerospace greases are composed of a base oil, thickening agent, and various additives. The base oil may be synthetic or mineral, depending on the specific requirements of the application. Synthetic base oils are often preferred for their superior thermal stability and low-temperature fluidity. The thickening agents, such as lithium or calcium soaps, help maintain the grease’s consistency and improve its load-carrying capacity. Additives, including antioxidants, anti-wear agents, and corrosion inhibitors, further enhance the performance and longevity of the grease.
Applications in Space Equipment
The applications of aerospace grease in space equipment are diverse and extensive. One of the primary uses is in lubricating moving parts within spacecraft and satellites. For instance, actuators, bearings, gears, and hinges all rely on lubrication to function smoothly. Without effective lubrication, these components are prone to wear and failure, potentially jeopardizing entire missions.
Moreover, aerospace grease is indispensable in the robotic arms and mechanisms used in space exploration. These highly sophisticated devices must operate flawlessly over prolonged periods and under fluctuating conditions. Effective lubrication is vital to their sustained performance and precision.
In addition to mechanical components, aerospace grease finds applications in electrical systems. Certain types of aerospace grease possess dielectric properties, allowing them to insulate and protect electrical connectors from environmental contaminants and corrosion. This dual functionality is crucial in maintaining reliable electrical connections in the vacuum of space.
Challenges and Requirements
The development and application of aerospace grease are marked by several challenges and requirements. One of the foremost challenges is the temperature stability of the grease. Space environments can vary drastically in temperature, ranging from the extreme cold of shadowed areas to the intense heat of direct sunlight. Consequently, aerospace greases must exhibit stable performance across a broad temperature range.
Additionally, the vacuum conditions of space present unique difficulties. In a vacuum, outgassing can occur, in which volatile components of the grease evaporate, leading to degradation of the lubricant and contamination of the surrounding environment. Aerospace greases must therefore be formulated to minimize outgassing, ensuring they retain their properties and do not adversely affect other components.
Compliance with rigorous standards and certifications is essential for aerospace grease. Agencies such as NASA, the European Space Agency (ESA), and the Department of Defense (DoD) have established stringent criteria that greases must meet before they can be used in space missions. These standards assess various aspects, including thermal stability, load-carrying capacity, and resistance to oxidation and corrosion.
Innovations and Future Trends
The landscape of aerospace lubrication is continually evolving, driven by advancements in materials science and engineering. Recent innovations include the development of nano-additives, which enhance the performance characteristics of aerospace greases. These tiny particles can improve load capacity, reduce friction, and boost thermal stability, making them highly attractive for space applications.
Moreover, the advent of smart lubricants is on the horizon. These greases are capable of self-monitoring their condition, providing real-time data on their performance and any potential degradation. This capability could usher in a new era of predictive maintenance, where issues are identified and addressed before they lead to equipment failure.
Another promising direction is the use of ionic liquids as lubricants. These liquids are known for their excellent thermal stability, low volatility, and remarkable lubricating properties. While still in the research phase, ionic liquids hold significant potential for revolutionizing aerospace lubrication.
Conclusion
In summary, aerospace grease plays a pivotal role in ensuring the smooth and reliable operation of space equipment. Its specialized composition allows it to withstand the extreme conditions of space, making it an indispensable component in mechanical and electrical systems. Understanding the complexities and innovations within this niche field is essential for advancing aerospace technology and achieving long-term success in space missions. As research and development continue to propel the field forward, the future of aerospace lubrication looks both exciting and promising.
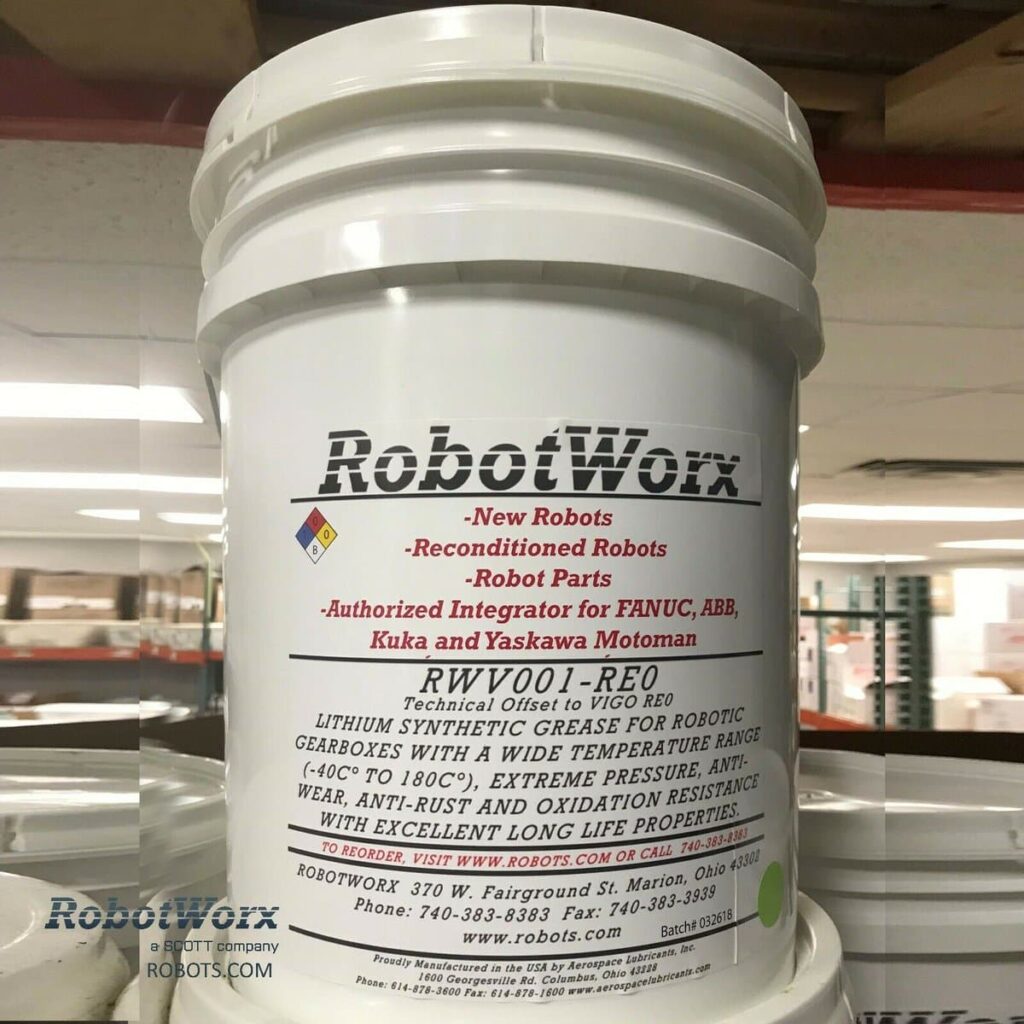