Introduction
Aerospace grease is a specialized lubricant applied to various components and systems within aircraft and spacecraft. It plays a crucial role in ensuring the smooth operation and longevity of these high-performance machines. Given the unique and often extreme conditions faced by aerospace applications, the choice of grease is fundamental to the safety, reliability, and efficiency of aviation operations. This article provides an introduction to aerospace grease, detailing its importance, types, selection criteria, and maintenance practices, to offer a comprehensive understanding of this pivotal material.
The Importance of Aerospace Grease
In the aerospace industry, the performance and safety of components are paramount. Aerospace grease serves as a lubricant that drastically reduces friction and wear between moving parts, which is vital for both mechanical efficiency and component longevity. Additionally, it acts as a sealant to keep contaminants such as dust, moisture, and corrosive elements out of delicate parts. This function is particularly significant since aircraft and spacecraft are exposed to a wide range of extreme environments, including high altitudes, varying pressures, and temperatures ranging from extremely high to extremely low.
Types of Aerospace Grease
Various types and formulations of aerospace grease have been developed to meet specific operational requirements. The selection depends heavily on the application and the environmental conditions in which the grease will be used. Below are some commonly used types of aerospace grease:
1. Mineral Oil-Based Grease: A traditional choice, mineral oil-based greases are cost-effective and provide adequate lubrication for standard conditions. However, they may not perform well under high thermal stress.
2. Synthetic Grease: Made from synthetic oils, these greases offer superior performance over a broader range of temperatures and conditions. They are particularly suitable for high-speed bearings and other critical components.
3. Silicone Grease: Known for their excellent thermal stability and resistance to water and oxidation, silicone-based greases are highly effective in extreme temperature environments. They are often used in applications where a wide operating temperature range is present.
4. Fluorinated Grease: These greases are designed for highly specialized applications requiring exceptional chemical inertness and durability. They offer outstanding resistance to solvents, fuels, and extreme temperatures, making them ideal for aerospace components exposed to harsh conditions.
Selection Criteria for Aerospace Grease
Selecting the appropriate aerospace grease involves several key considerations to ensure the effectiveness and safety of the lubricant. These criteria include:
Temperature Range: The grease must perform adequately within the temperature extremes expected in the aircraft’s operating environment. A grease that can withstand high temperatures may not be effective in sub-zero conditions, so selecting a grease with a suitable temperature range is crucial.
Load-Bearing Capability: The grease must be able to handle the loads and stresses it will encounter. This includes consideration of factors such as pressure, shear forces, and potential impact loads that could affect the integrity and performance of the grease.
Compatibility: The selected grease should be compatible with the materials it will contact, including metals, plastics, and seals. Incompatibility can lead to degradation, swelling, or embrittlement of the materials.
Resistance to Contaminants: The selected grease should provide a barrier to contaminants and resist oxidation, corrosion, and chemical degradation to maintain efficacy over time.
Longevity and Stability: Aerospace grease should demonstrate long-term stability and performance, minimizing the need for frequent reapplication and maintenance.
Application and Maintenance Practices
Proper application and maintenance are critical to maximize the effectiveness of aerospace grease. Here are some best practices:
Pre-Cleaning: Before applying grease, ensure that the surfaces and components are thoroughly cleaned to remove any contaminants. This step helps prevent impurities from compromising the effectiveness of the lubricant.
Correct Application: Use the appropriate tools and techniques for applying the grease. Over-application or under-application can lead to ineffective lubrication and potential issues. Follow manufacturer recommendations for quantity and method of application.
Regular Inspections: Routine inspections help identify potential issues early. Check for signs of grease degradation, contamination, or insufficient lubrication. Address any issues promptly to maintain optimal performance.
Environmental Considerations: Store grease in conditions that prevent contamination and degradation. Protect the grease from extreme temperatures and moisture during storage and transportation.
Reapplication and Re-greasing: Some components may require periodic re-greasing to maintain efficacy. Follow the maintenance schedule recommended by the manufacturer to ensure continued protection and lubrication.
Conclusion
Aerospace grease is an essential component in the smooth operation and longevity of aircraft and spacecraft. Understanding the types of grease available, the criteria for selecting the correct one, and the best practices for application and maintenance is crucial for maintaining safety and performance. By focusing on these aspects, aerospace operators can ensure that their machines operate efficiently under various conditions, ultimately contributing to the safety and reliability of aviation and space missions.
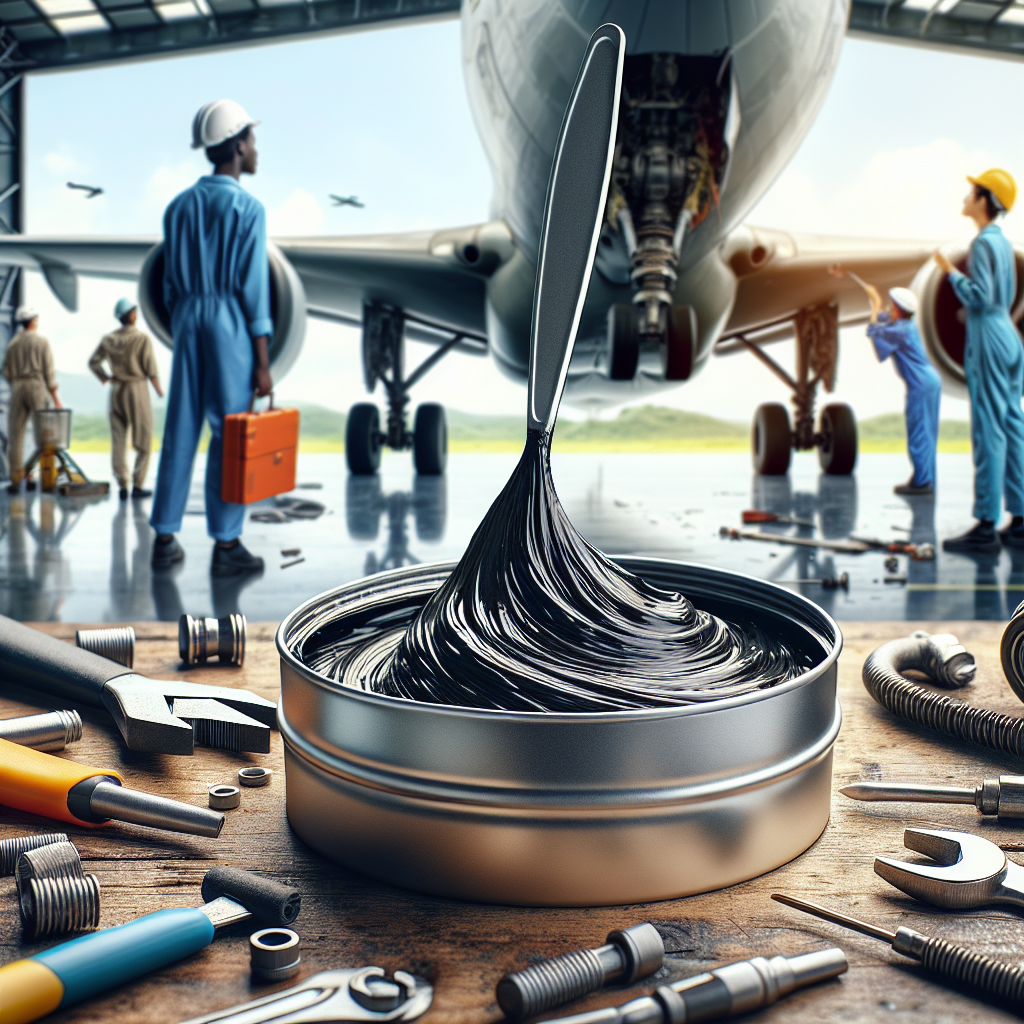