Introduction to Multipurpose Aerospace Grease
The aerospace industry demands materials that meet stringent performance and safety standards. One such essential material is multipurpose aerospace grease. This high-performance lubricant is crucial for ensuring the reliability and efficiency of aircraft components under extreme conditions. Understanding its properties, applications, and benefits can shed light on why it plays a vital role in aviation and aerospace operations.
Understanding Multipurpose Aerospace Grease
Multipurpose aerospace grease is a specially formulated lubricant designed to meet the unique demands of aerospace environments. Unlike conventional greases, aerospace greases are engineered to withstand extreme temperatures, high pressures, and various environmental conditions that aircraft are exposed to during flight. Typically composed of a base oil, thickener, and performance-enhancing additives, these greases ensure optimal performance and longevity of aircraft components.
Key Properties of Aerospace Grease
Aerospace grease exhibits several key properties that differentiate it from other types of lubricants. First and foremost, it possesses excellent thermal stability, enabling it to function effectively over a wide temperature range. This is particularly important in aerospace applications where temperatures can vary drastically. For instance, aircraft operating at high altitudes or in outer space face extremely low temperatures, while those maneuvering at high speeds generate significant heat.
In addition, aerospace greases offer exceptional resistance to oxidation and corrosion. This ensures that the lubricant maintains its integrity and effectiveness even in harsh environmental conditions. The presence of performance-enhancing additives further augments the grease’s ability to resist water washout, chemical exposure, and mechanical wear. These combined properties make aerospace grease indispensable in maintaining the reliability and performance of aircraft systems.
Applications in Aerospace Industry
The versatility of multipurpose aerospace grease makes it suitable for a wide range of applications within the aerospace industry. Some of the primary uses include lubricating bearings, gears, actuators, and various mechanical joints. For example, in aircraft engines, grease is essential for lubricating bearings to reduce friction and wear. This not only enhances the efficiency of the engine but also prolongs its operational life.
Furthermore, aerospace grease is used in landing gear systems to ensure smooth and reliable operation during takeoffs and landings. The dynamic nature of these systems necessitates a lubricant that can handle significant stress and varying environmental conditions. Similarly, in avionics and electrical systems, specialized greases protect connectors and switches from moisture and corrosion, thereby maintaining optimal electrical conductivity and functionality.
Performance Benefits
The use of multipurpose aerospace grease offers several performance benefits that are crucial for the safety and functionality of aircraft. One of the primary advantages is reduced maintenance frequency. High-quality aerospace greases have longer re-lubrication intervals due to their superior durability and resistance to degradation. This translates to lower maintenance costs and increased aircraft availability.
Another significant benefit is enhanced operational efficiency. By reducing friction and wear in mechanical components, aerospace greases contribute to the overall efficiency of aircraft systems. This can lead to improved fuel efficiency and reduced operating costs. Additionally, the ability of these greases to withstand extreme temperatures and environmental conditions ensures consistent performance, enhancing the reliability and safety of the aircraft.
Selection Criteria
The selection of appropriate multipurpose aerospace grease is a critical process that involves several considerations. First, it is essential to evaluate the specific requirements of the application, such as temperature range, load-bearing capacity, and exposure to environmental factors. Manufacturers typically provide detailed specifications and performance data to aid in this selection process.
Compatibility with materials is another important factor. Aerospace components may be composed of various metals, plastics, and elastomers. The selected grease must be compatible with these materials to avoid any adverse chemical reactions or degradation. Additionally, regulatory compliance is a key consideration. Aerospace greases must meet industry standards and certifications to ensure they are suitable for use in aviation applications.
Maintaining Quality and Reliability
To ensure the continued effectiveness of multipurpose aerospace grease, it is essential to follow best practices for storage, handling, and application. Proper storage conditions, including appropriate temperature and humidity levels, help prevent contamination and degradation of the grease. Handling procedures should minimize exposure to contaminants such as dust, dirt, and moisture. Additionally, using the correct application techniques ensures optimal distribution and performance of the grease in the intended components.
Regular monitoring and testing of aerospace grease are also vital for maintaining quality and reliability. This involves periodic analysis of the grease’s physical and chemical properties to detect any signs of degradation or contamination. Early detection of potential issues allows for timely corrective actions, ensuring the continued performance and safety of the aircraft.
Conclusion
Multipurpose aerospace grease is an essential component in the aerospace industry, providing the necessary lubrication and protection for critical aircraft systems. Its unique properties, including thermal stability, oxidation resistance, and mechanical durability, make it indispensable for maintaining the reliability and efficiency of aircraft operations. By understanding its applications, benefits, and selection criteria, industry professionals can ensure the optimal performance and longevity of their aerospace components. Ultimately, the judicious use of high-quality aerospace grease contributes to the safety, reliability, and cost-effectiveness of aviation endeavors.
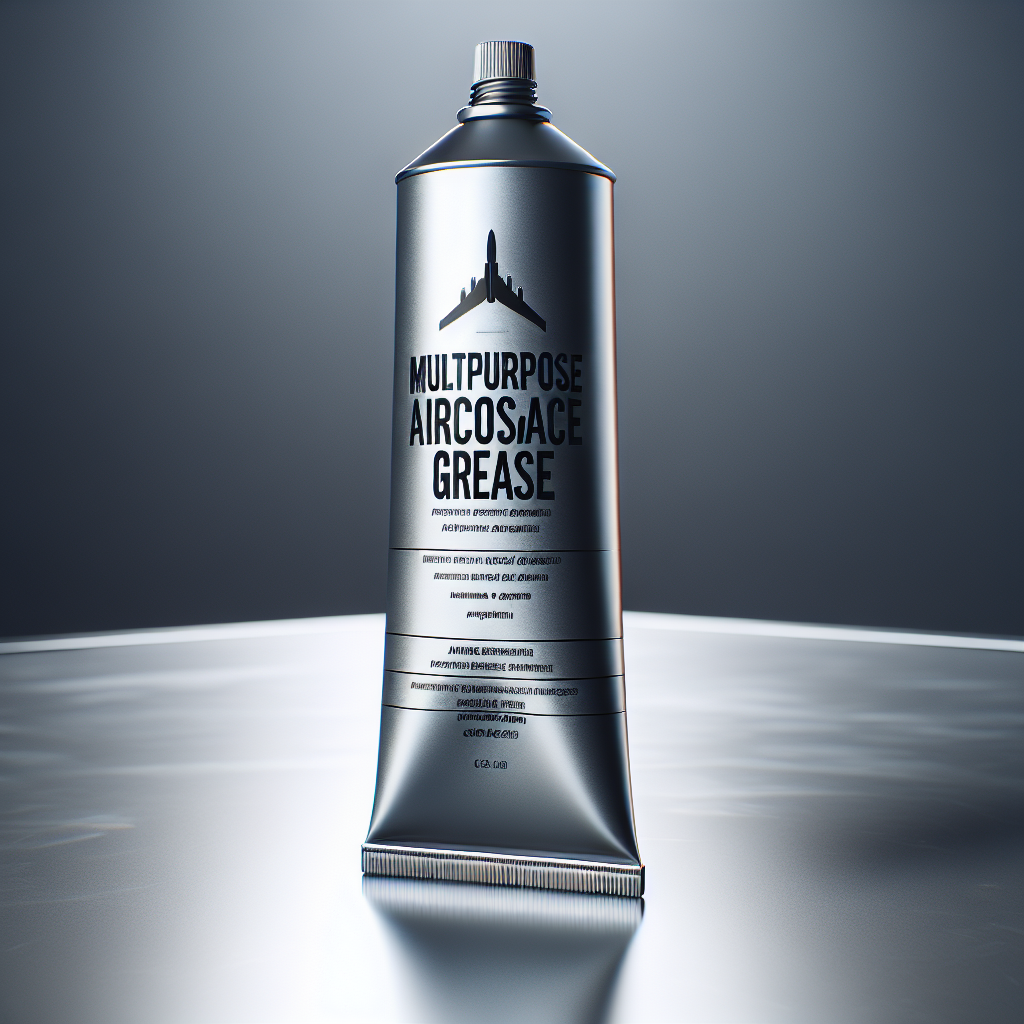