Introduction
Grease gun tools have become indispensable in both residential garages and professional workshops. These tools are essential for maintaining machinery, vehicles, and various mechanical systems. By providing precise lubrication, grease guns help ensure the longevity and efficiency of moving parts. In this article, we will explore the different types of grease guns, their primary uses, and why they are crucial for mechanical maintenance. Additionally, we will provide guidance on selecting the right grease gun and offer tips for effective use and maintenance.
Types of Grease Guns
There are several types of grease guns available on the market, each designed to meet specific lubrication needs. The three primary types include hand-operated, pneumatic, and battery-powered grease guns. Understanding the differences between these types will enable you to select the best tool for your requirements.
Hand-Operated Grease Guns
Hand-operated grease guns are the most basic and commonly used type. They are divided into lever and pistol-grip models. Lever grease guns require the user to manually pump a lever to dispense grease, allowing for precise control over the amount of grease applied. Pistol-grip grease guns, on the other hand, use a trigger mechanism and are generally easier to operate with one hand, making them suitable for tight spaces.
Pneumatic Grease Guns
Pneumatic grease guns use compressed air to drive the grease out of the tool. This type is ideal for tasks requiring a high volume of grease or repetitive applications. Pneumatic grease guns are powerful and efficient, making them a popular choice in commercial and industrial settings. However, they require an air compressor, which adds to the initial investment and overall setup complexity.
Battery-Powered Grease Guns
Battery-powered grease guns offer the convenience of cordless operation combined with the power of pneumatic models. These grease guns use rechargeable batteries to provide consistent pressure and are suitable for both light and heavy-duty applications. Battery-powered grease guns are ideal for users who need mobility and flexibility without being tethered to an air compressor.
Primary Uses of Grease Guns
Grease guns are versatile tools used in a variety of applications. Their primary function is to provide lubrication to mechanical parts, ensuring smooth operation and reducing friction and wear. Some common uses for grease guns include lubricating automotive parts, industrial machinery, agricultural equipment, and heavy-duty construction machinery.
In automotive maintenance, grease guns are used to lubricate components such as ball joints, tie rod ends, and bearings. In industrial settings, they help maintain the efficiency of machinery by ensuring that parts like gears and chains are well lubricated. For agricultural equipment, grease guns are essential for maintaining the performance of tractors, plows, and harvesters. In the construction industry, they ensure that heavy equipment, such as excavators and loaders, operate smoothly and efficiently.
Selecting the Right Grease Gun
Choosing the right grease gun depends on several factors, including the specific application, frequency of use, and available budget. When selecting a grease gun, consider the following factors:
1. **Type of Grease Gun**: Decide between hand-operated, pneumatic, or battery-powered models based on your needs. For infrequent, light-duty tasks, a hand-operated grease gun may suffice. For more demanding applications, pneumatic or battery-powered models are better suited.
2. **Capacity and Output**: The grease gun’s capacity refers to the amount of grease it can hold, while its output indicates how much grease is dispensed per stroke or trigger pull. Consider the volume of grease required and the precision needed for your tasks.
3. **Ease of Use**: Ergonomic design and ease of operation are essential, especially if the tool will be used frequently. Look for features such as comfortable grips, easy loading mechanisms, and clear instructions.
4. **Build Quality**: Durable construction ensures that the grease gun can withstand regular use and harsh working conditions. High-quality materials and robust design are crucial for long-term reliability.
Effective Use and Maintenance
To maximize the efficiency and lifespan of your grease gun, it is essential to use and maintain it properly. Here are some tips:
1. **Read the Manual**: Familiarize yourself with the manufacturer’s instructions and guidelines for your specific grease gun model. This will ensure proper use and prevent potential damage.
2. **Choose the Right Grease**: Use the appropriate type of grease for your application. Different machinery and components may require specific types of grease with unique properties and viscosities.
3. **Regular Cleaning**: Keep the grease gun clean to prevent contamination and ensure smooth operation. Wipe down the exterior, and clean the nozzle and fittings regularly.
4. **Inspect for Wear and Damage**: Periodically check the grease gun for signs of wear and damage. Replace any worn-out parts promptly to avoid compromising performance.
Conclusion
Grease gun tools play a critical role in the maintenance and longevity of various mechanical systems. By understanding the different types, primary uses, and selection criteria, you can make an informed decision and choose the right tool for your needs. Proper use and regular maintenance will ensure that your grease gun remains an effective and reliable asset in your toolkit. Whether for automotive, industrial, agricultural, or construction applications, a high-quality grease gun is a valuable investment that enhances efficiency and prevents costly breakdowns.
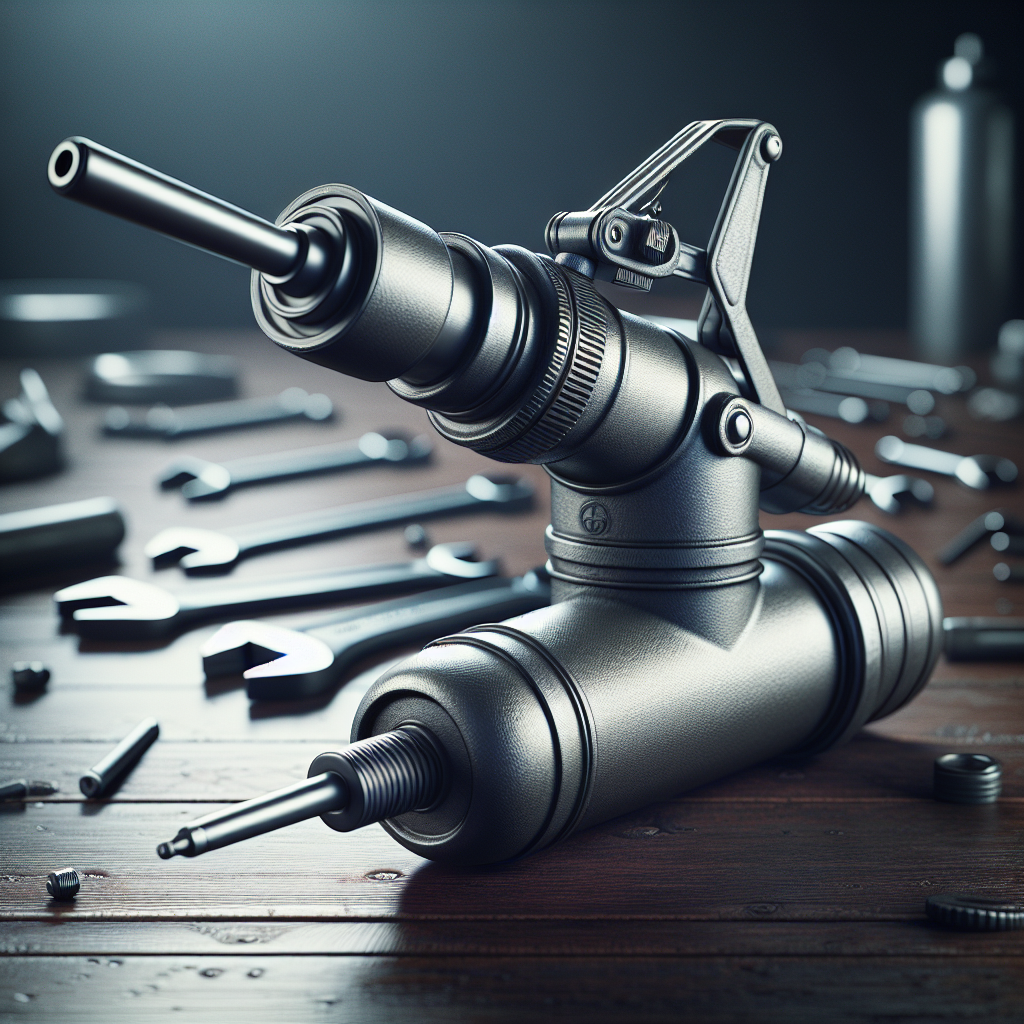